One of the most common warehouse and distribution center challenges is lack of space. Square footage isn’t cheap and it’s important for your business that you utilize your storage space effectively. Cost effective changes to your racking system or material handling equipment can increase the number of pallet positions in your space and help you operate more efficiently.
When moving to high-density storage, you’ll need to evaluate your priorities in terms of density, selectivity, and cost. Because increasing density usually means decreasing selectivity, it’s imperative to find the balance that works for your needs. Packing a warehouse with pallets from floor to ceiling, for example, is considered a high-density solution, which results in very low selectivity. It could require dozens of moves to access the inventory you need.
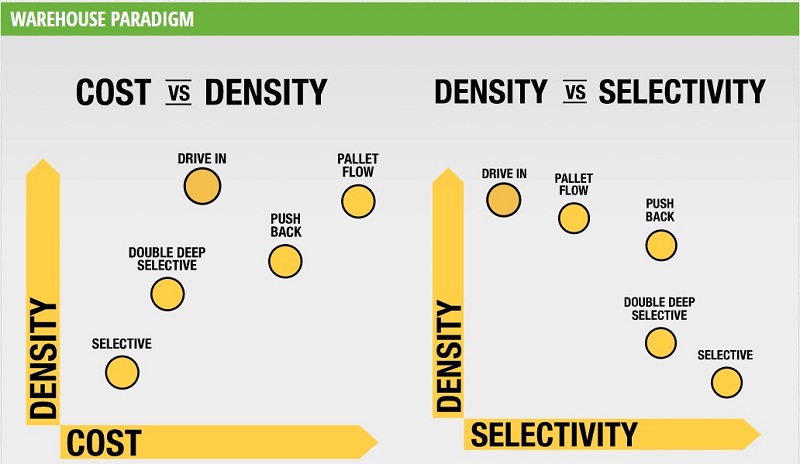
At Engineered Products, a Papé company, we call this the warehouse paradigm. Our goal is to help you determine the right balance of cost, density, and selectivity to store more pallets in the same space and move more loads per hour. Let’s go over how we can help and some of the racking options available.
HOW WE HELP
To better understand your specific business needs, our product team will start by asking you the following questions:
- What is the flow of the pallet in your warehouse or distribution center?
- Do you case pick, piece pick, or full pallet pick?
- What is your pallet type/size/weight?
- How many SKUs do you stock?
- How often do you turn your product?
- Do you use LIFO or FIFO inventory management?
- Is your product date stamped?
- Do you have a conditioned operating environment?
- What storage capacity do you have now and what storage capacity would you like to have?
- How many pallet positions do you have now?
Your answers to these questions will help us understand your needs so we can make the best recommendations to solve the challenges you’re facing. Our product specialists will use the information you provide or visit your facility for a pallet flow assessment to guide you to the best racking and equipment solution from the options below.
PALLET RACKING OPTIONS
CONVENTIONAL SELECTIVE RACK
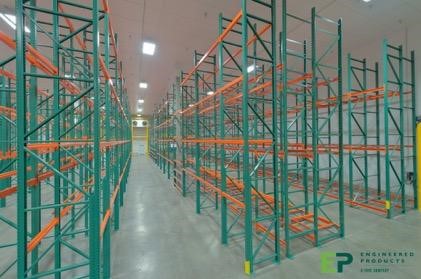
For businesses that require easy access to every pallet, we recommend conventional selective rack. It provides 100% selectivity. Selective rack is one of the lowest cost options for warehouse pallet racking and as a result is the most commonly found racking in warehouses around the world. For customers who already have conventional selective rack and would like to increase density without buying all new racking, adjusting the aisle widths will increase capacity. Switching to narrow aisle forklifts can reduce aisle widths by up to 100 inches, allowing for additional racking in the same warehouse space.
ADVANTAGES:
- High selectivity
- FIFO inventory management
- Lowest cost racking
DISADVANTAGES:
- Low density
- Limited storage height
DOUBLE DEEP RACK
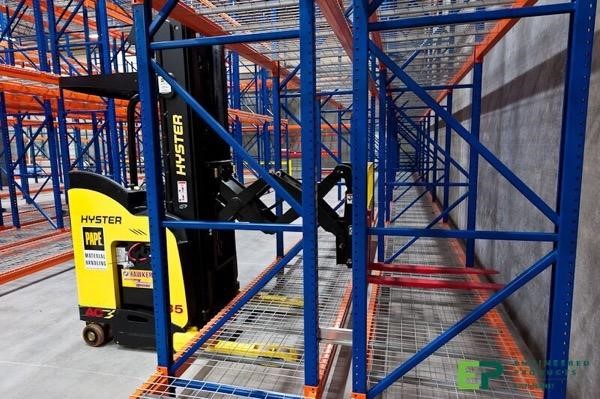
Double deep racking stores pallets two rows deep instead of one. Depending on your warehouse layout, this option can increase storage by 10-15%. Because it reduces selectivity, we recommend double deep racking for warehouse inventory with a long-term shelf life. For customers who would like to continue to use their existing lift trucks, telescopic attachments allow standard forklifts to operate as reach trucks.
ADVANTAGES:
- Increase storage capacity
- Low cost
DISADVANTAGES:
- LIFO inventory management
- Low selectivity
- Specialty forklifts/attachments required
DRIVE IN OR DRIVE THRU RACK
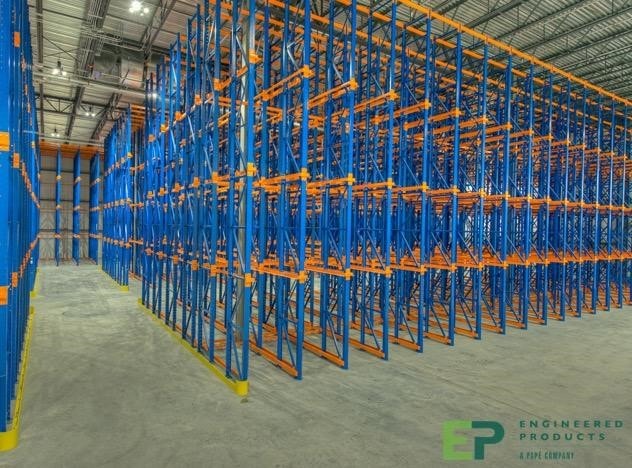
The highest density solutions available, drive in or drive thru pallet racking can increase pallet capacity by up to 75% depending on your warehouse layout. Racks are back-to-back without the need for aisles. With drive in racking, forklifts add and remove inventory from the same entry point for LIFO inventory management. With drive thru racking, pallets are added and removed from separate access points for FIFO inventory management. No special forklifts are required to use drive in or drive thru racking.
ADVANTAGES:
- Very high density
- Cost effective
DISADVANTAGES:
- Low selectivity
- Racks more at risk for damage
- Additional operator training required
PUSH BACK RACK
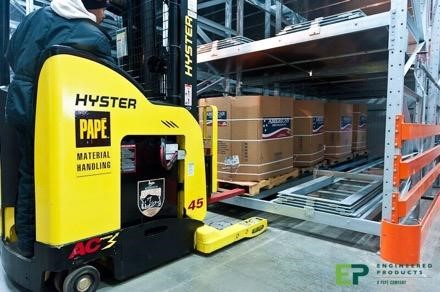
Push back pallet racking offers a very high-density LIFO inventory management system. In push back racking, pallets are loaded onto carts on slightly inclined rails. As each pallet is loaded it pushes back the pallet loaded before it. When pallets are removed, the incline drops the pallets behind into place. Like drive in or drive thru racking, no specialized lift trucks are required. Because operators do not have to drive into the rack to access pallets, push back rack systems typically result in less wear and tear.
ADVANTAGES:
- High density
- No specialty equipment needed
- Forklifts don’t enter rack
DISADVANTAGES:
- High cost
- LIFO inventory management
PALLET FLOW RACK
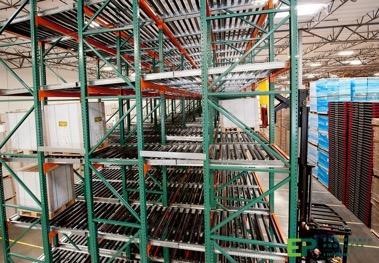
Pallet flow racking is like drive in racking in terms of inventory capacity, but it does not require operators to drive into the rack to access pallets. While it has a higher upfront cost, ongoing maintenance is likely to be lower. This type of rack features rollers so when a pallet is removed from the unloading end, the pallets behind automatically move forward to the end of the rack. The depth of the rack is only limited by the size of the warehouse.
Advantages:
- FIFO management
- Very high density
- Automatic product rotation
- No specialty forklifts required
- Lower risk of rack damage
Disadvantages:
- High cost
- High-quality pallets required
- Low selectivity
Let us help you find the right warehouse solutions and layout for your needs. Contact your nearest Engineered Products location for a free pallet flow assessment. We’ll provide insights that help you make money and save money.